(This article was first emailed on April 19th, 2021 to fans who had registered an interest in finding out more about our Tricorder.)
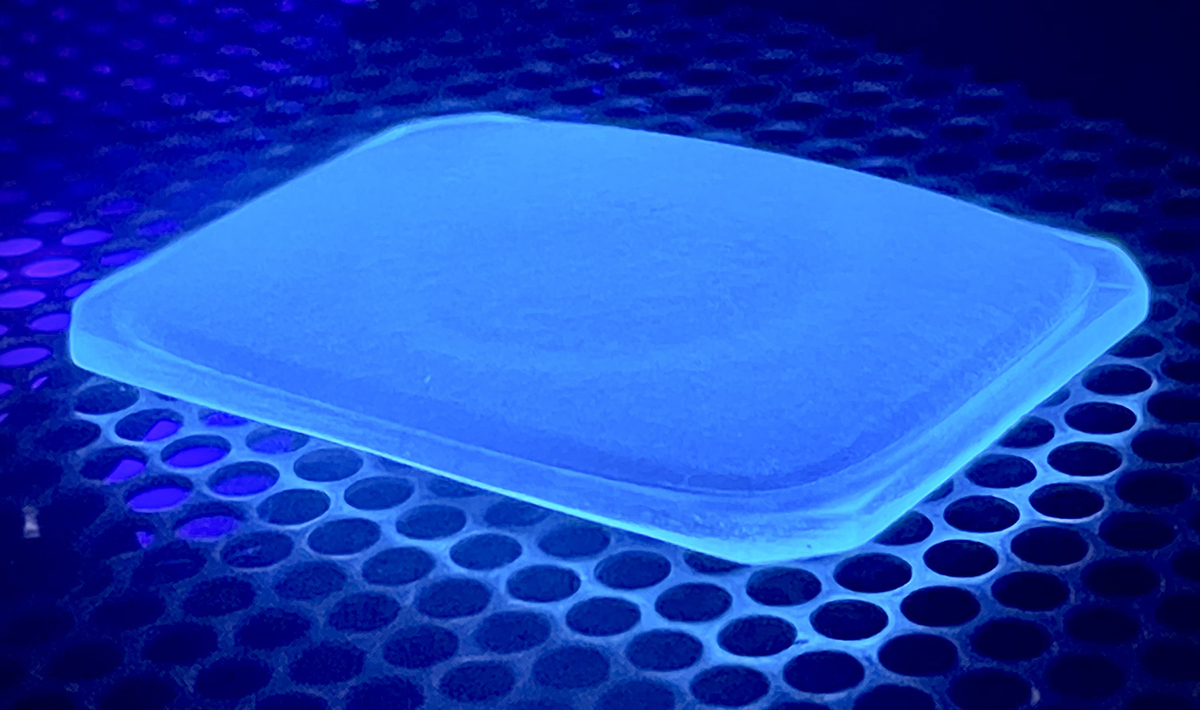
UV curing a clear resin 3D print of the display glazing panel
3D printing is a relatively new technology which has been hugely beneficial to almost all engineering and product development activities, for example in space, in the automotive industry, and in giving people superpowers. When stereolithography first began to widely used in industry in the mid-1990s, fragile, small parts could cost thousands of dollars, but there is now a wide variety of 3D-printing technologies and materials, and the cost has reduced dramatically, such that 3D printing is now accessible to almost anyone.
Our tricorder CAD was a constantly evolving mechanical design for well over a year, as we pulled together all the elements that we wanted to fit inside the skin of this iconic prop. Several of the early mechanical concepts required physical testing before being developed into a design that could be manufactured and 3D printing was a key part of this process. 3D printing allows us to quickly produce real parts in practically any shape we like, which could be difficult or even impossible to injection mould. This is helpful, as we can get a concept made quickly which allows the parts to be tested in mechanisms before being tweaked and developed into models that are designed as production parts. Once the mechanical concept is tested, then the parts have to be designed so that they will be manufacturable in an injection mould tool with the associated limitations and essential draft angles.
The tricorder CAD needed refinement right up to the point where the design was frozen so that injection moulding tools could be cut. Injection mould tooling is tremendously expensive, and once the tooling is being made, further changes are difficult and costly to make. Of course, if there are issues that crop up in the realisation of the design, sometimes there is no choice but to revise the design after the tooling has been started or even completed.
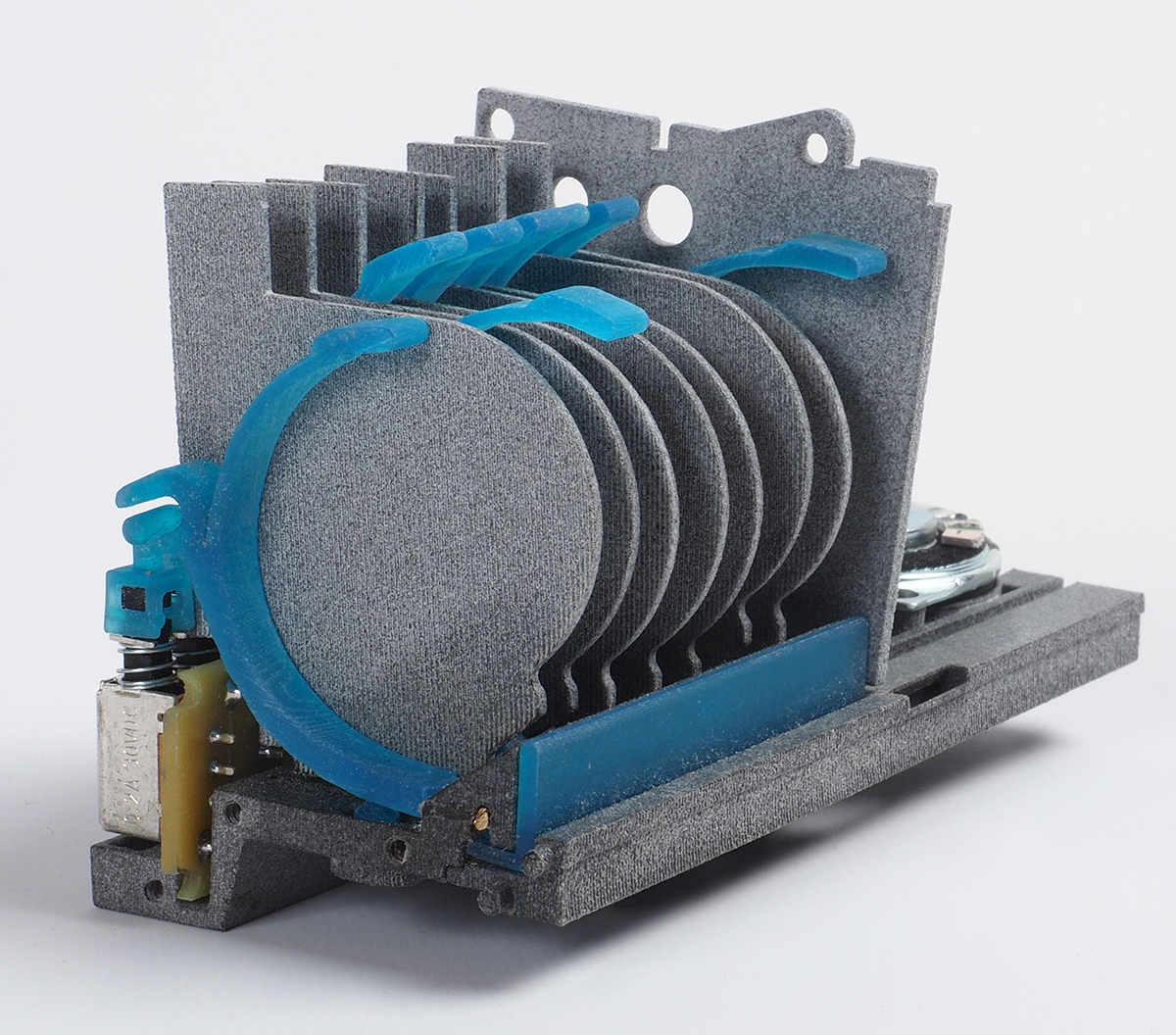
“Tough” SLA disc ejector mechanism v4
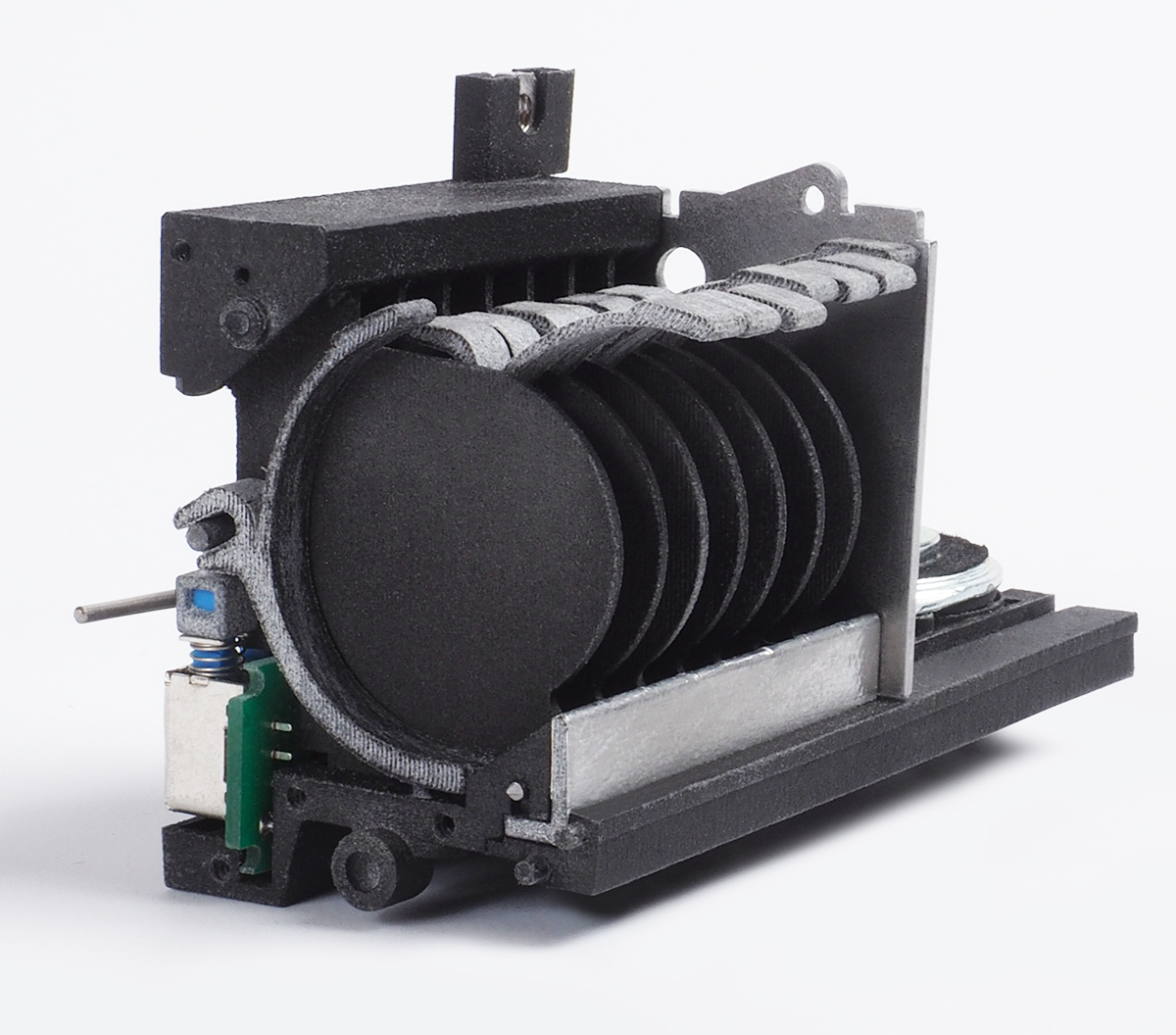
MJF Nylon, improved disc ejector v7
To minimise the potential for changes this late on in the process and also, from the earliest point possible, to find out if the CAD design would work in the real world, each of the components have been 3D printed, often multiple times. 3D printing the tricorder has been critical in realising the design and understanding fully how it will fit together, be built on the production line and actually work in the hands of a user. Seeing the geometry turned into real 3D printed components assembled, all mechanically slotting into each other, truly brings the tricorder to life. After many months of working through the CAD, it’s exciting to see the model actually working and makes the product very real in every sense.
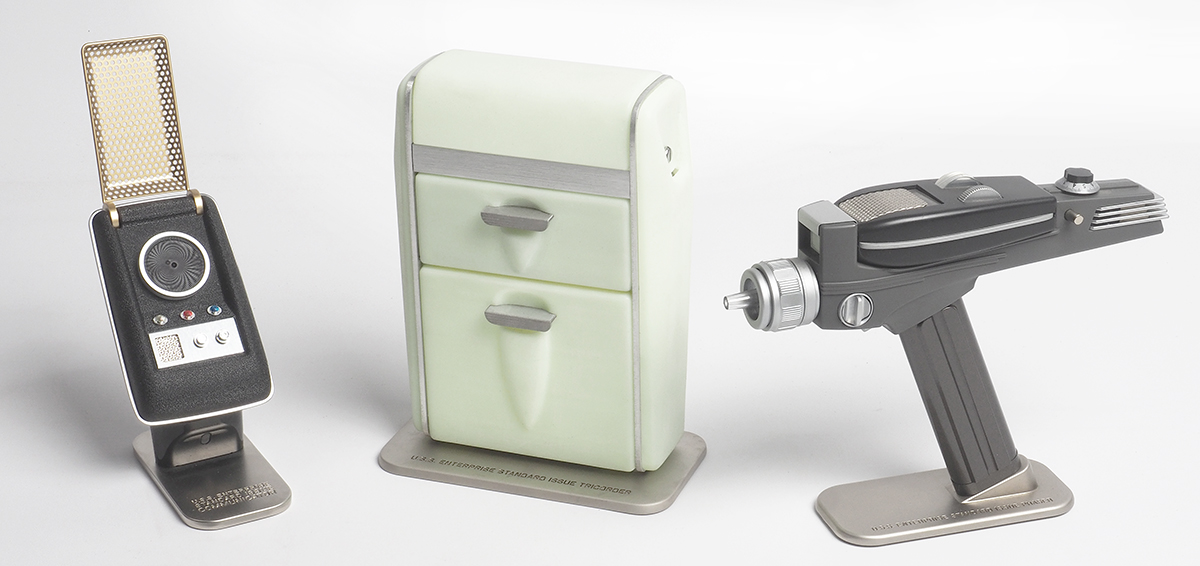
A late-stage 3D print: nearly there, but still some improvement tweaks to make
But exactly how did we get from a virtual tricorder design to a real-world printed mechanical prototype model?
Initially, the tricorder component files were created and stored as a parasolid geometric modeling kernel; a format used by SolidWorks. In order to 3D print a given tricorder component, the file is output as an STL file which can be imported into the 3D printer’s native software where the orientation is chosen and supports (scaffold structures to hold overhangs) are created. This semi-automated process generates a position and support scaffold but enables the user to move or add supports and alter the orientation of the part with respect to the print surface in order to get the best finish on the most visible or most mechanically critical area of the part. Often the best orientation is not what you might expect. For the tricorder’s screen cover, with its thin low-profile section, from a speed and simplicity perspective, it would have seemed obvious to lay it flat on the printer bed. However, to minimise the number of supports attached to the middle of the screen, and avoid contour-stepping on the gently curved surfaces, it was turned to stand upright, thus producing a much better-looking and functioning part. Once the part to be printed looks as though it will print without errors, the 3D printer converts the file to a series of 0.025 mm slices which are then output as a layer-by-layer set of g-code commands for the 3D printer.
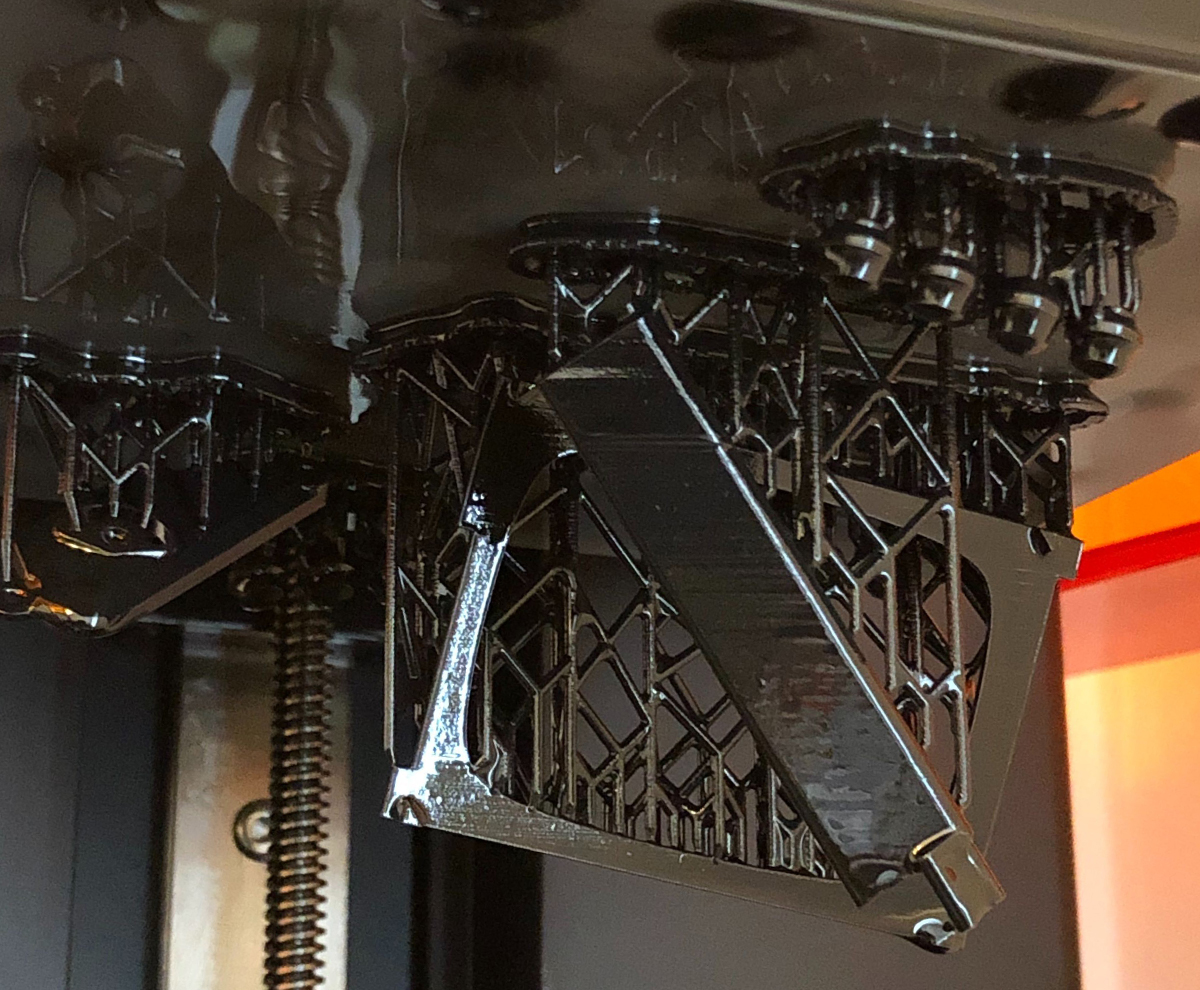
Screen bezel, disc ejector glamour bar and buttons emerge from the SLA resin bath
We have a Formlabs SLA (stereolithography) machine which we used to print the tricorder prototypes due to its superior resolution. A tray of liquid resin is cured, one 0.025 mm slice at a time, by an ultraviolet (UV) laser, allowing the model to grow out of the resin reservoir layer by layer. Based on the mechanical properties we need, we have a selection of resins with different properties to choose from depending on which tricorder part is being printed, although our printer has a 145 x 145 x 170 mm print volume which makes it only suitable for smaller, more detailed parts. For the display glass and LED light pipes, we used a clear resin that can be polished to make it transparent. For the first mechanical trials of the disc ejector mechanism we used a blue resin called ‘Tough’ which has more durable and resistant properties, similar to a production plastic.
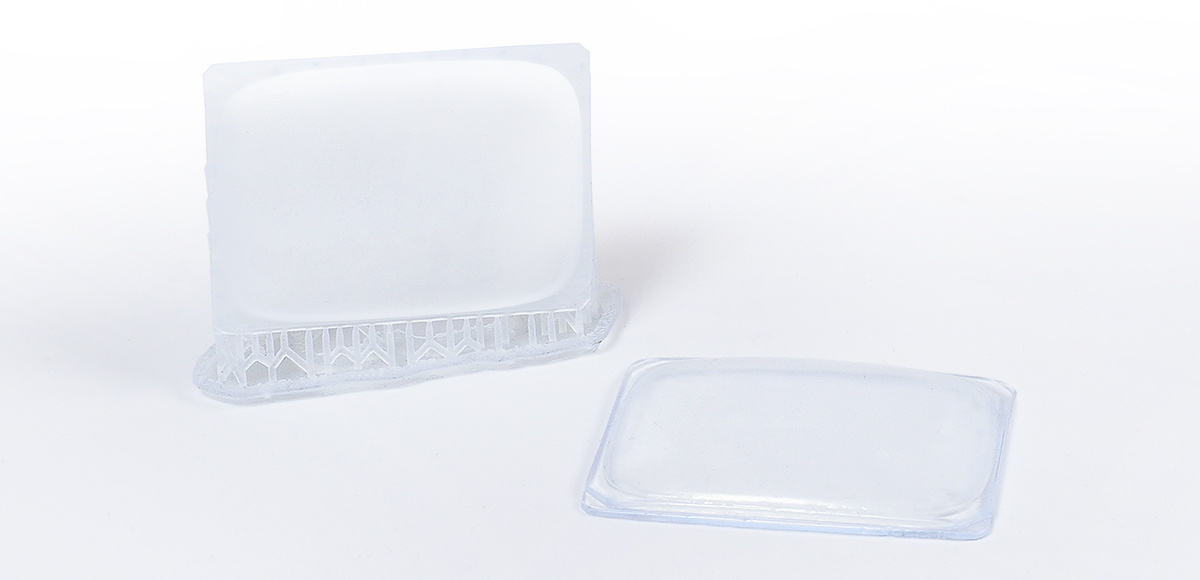
Clear SLA resin display glazing panel prints, angled to reduce finishing
Despite the accuracy, each SLA part requires a great deal of finishing. Newly printed parts must be carefully washed and then cured using a UV light chamber.
Once cured, the part must have its scaffold support structure removed. As the support structure is the same material as the model itself, if a blemish-free surface is necessary, then this stage can be very time-consuming.
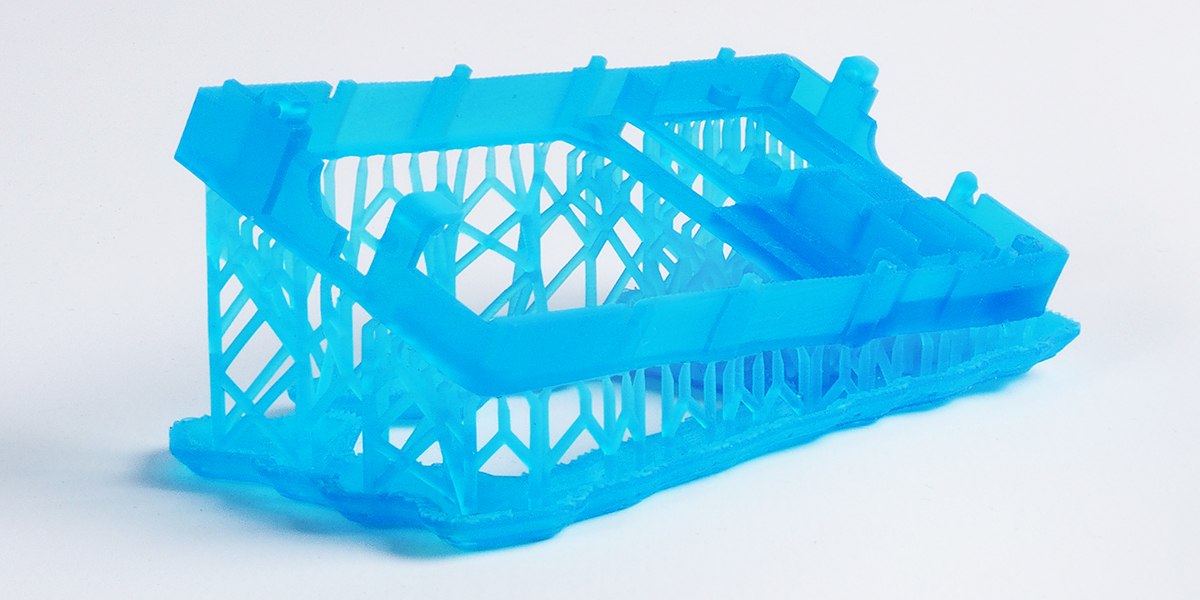
Early display support frame printed in Tough Resin V5
We also have various FDM (fused deposition modelling) machines to use for larger, less critical parts, or if we need to choose a specific 3D printing material to mimic the tough, flexible properties of the injection moulding plastic like ABS for example. FDM machines are the most common 3D printers because they are relatively simple, cheap, clean and easy to use. A reel of plastic filament is melted through a hot nozzle and applied layer by layer onto a platform. Components printed by the FDM process are generally good for block models and other more basic parts because they are quick, but the finish is not smooth, as the layer thickness is usually around 0.1 mm which shows as visible layer lines.
For some of the larger tricorder parts where we wanted a tough, resilient, but also accurate, print, we had to use an external service. For these parts we used HP’s Multi Jet Fusion (MJF) process to produce the highly accurate, thin, stiff and nicely finished panels needed for the tricorder’s doors and sides. Parts emerge from a fine powder bed as a modified inkjet printer first prints layers of a binding agent, then rapidly solidifies the composite with heat. The powder bed supports the part during printing so no support scaffold is needed, greatly simplifying the amount of component surface finishing required when the printing is complete.
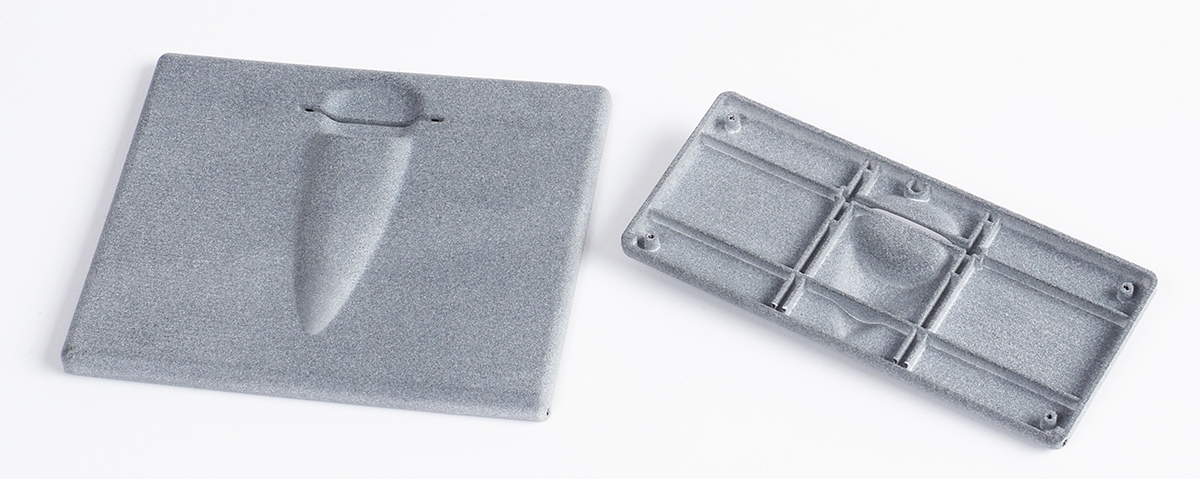
Multi Jet Fusion door panels, printed by Materialise, arrive ready to assemble onto the model
It’s not only us that need to see and feel the tricorder: our factory also makes use of rapid prototyping and Stratasys PolyJet 3D printing machines to get a better understanding of what they are going to have to manufacture. A fully working prototype is essential for the factory to test the fit and build sequence and make sure that the CAD really works before tool cutting is started. There are many aspects of the design that are very difficult to gauge from just looking at CAD on a screen or by testing functions with simulation software – for example, how bundles of cables are routed, what the detents on the hood opening action feel like in operation, or how the range of internal state sensors perform together. It is usual for these factory models to be expensive and time-consuming to build and, more often than not, the process is repeated a number of times whilst the design is refined as issues are discovered and ironed out in subsequent revisions, which then also need testing. They are, however, a very necessary step towards full manufacture.
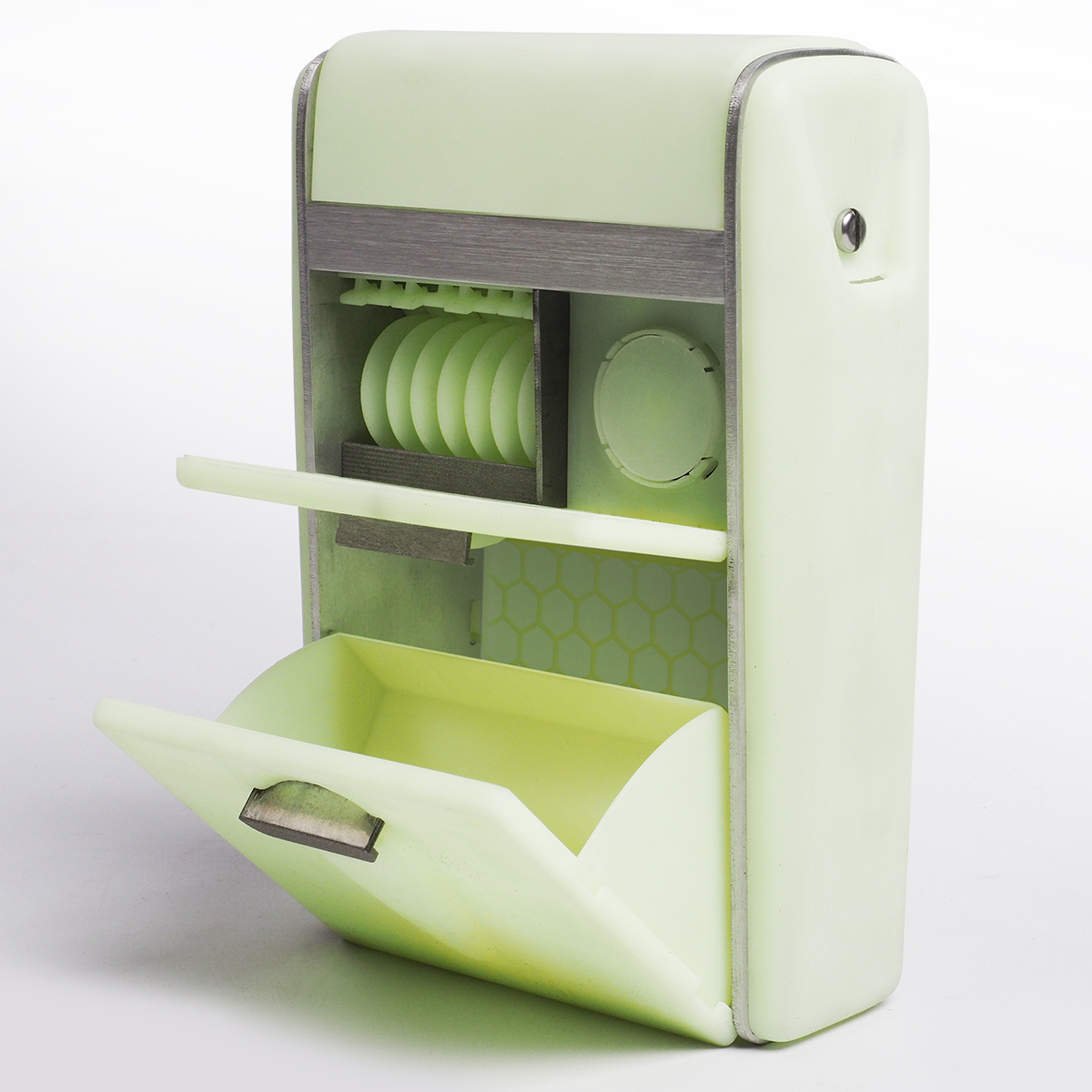
PolyJet 3D print produced by the factory. 3D printing is a very necessary step towards full manufacture
To make a fully working tricorder prototype, 3D printing can only get you so far. The tricorder is constructed from a range of different materials, and in addition to 68 injection moulded parts which can be 3D printed, there are 22 metal parts, a number of different sized screws, bolts, springs, and magnets, a hand-stitched leatherette strap, and more than 350 electronic components assembled on to six printed circuit boards.
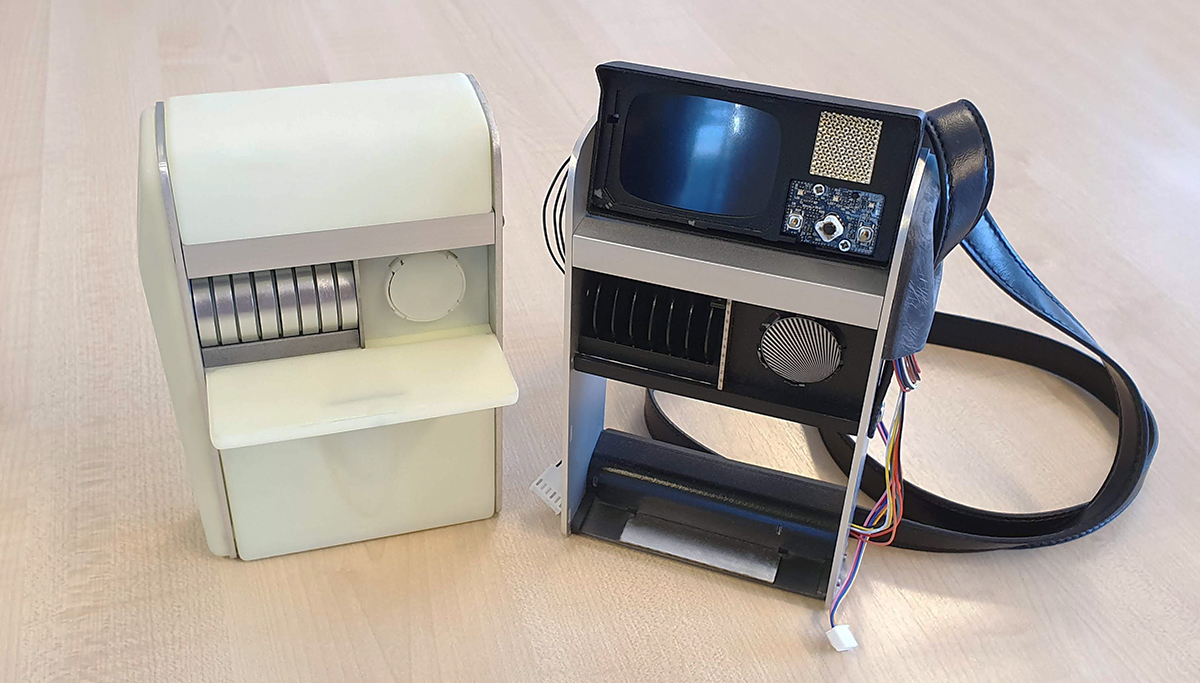
A combination of different rapid prototyping capabilities is needed to put together something as complex as the tricorder and to test how it is going to look, feel and function
Where it is easier or more accurate to do so, many of the metal parts are created using traditional CNC machining, laser or waterjet cutting. For the tricorder’s side frame plates, we had access to a laser cutter which allowed us to initially cut acrylic sheet to shape to create quick prototype models in order to test our initial design concepts. As soon as the design had been refined, the side plates were sent out to an external fabricator to be laser cut from aluminium. For some of the parts it was quicker to use some of our more traditional prop making skills and, when some angled handles were needed in short order for the prototype model, the basic shape was milled from stock, in-house, and finished by hand with a file.
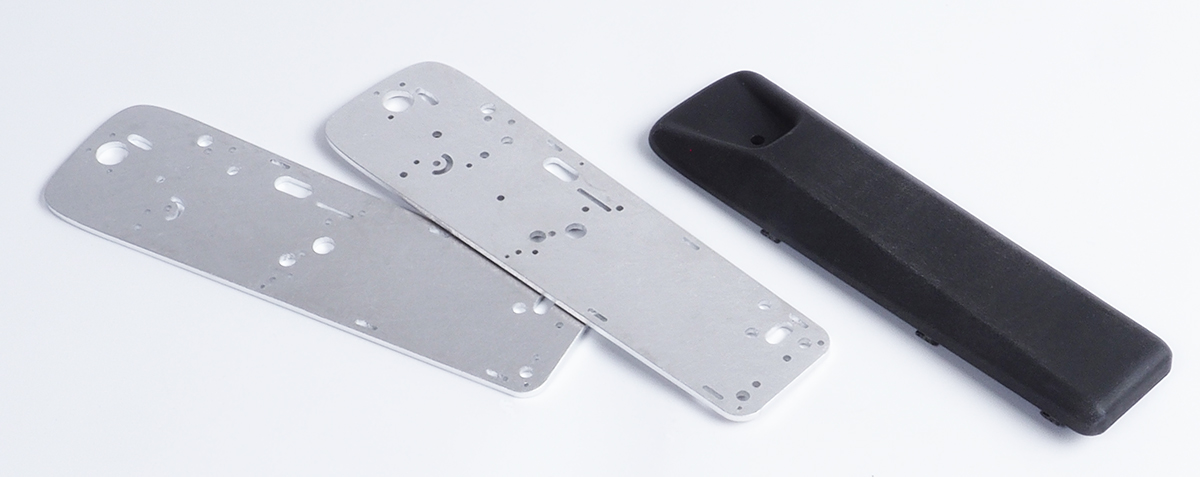
Laser-cut sheet aluminium side plates and Multi Jet Fusion side panel to test assembly concept
In fact, a file, sandpaper, a Dremel, scalpels and just about every other small model-making tool are not yet redundant and are employed throughout the 3D printing process as each part requires a significant amount of hand finishing.
So, while on the face of it, 3D printing direct from CAD files appears as though it might reduce the need for the craftsmanship that gave us some of our most cherished and iconic props from yesteryear, those traditional prop-finishing skills have not been entirely outmoded by the 3D printer. And, for now at least, there is still a huge degree of hand finishing required to build complex models such as the tricorder from 3D-printed components. Nevertheless, 3D printing is enabling us to get ever closer to creating prop replicas that truly embody the original intent of those gorgeous fully hand-made props from decades ago.
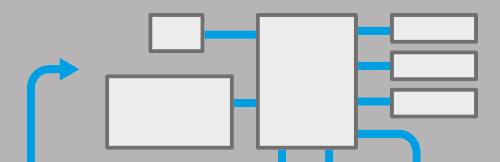
Coming next time
Functional blocks – working out how it will work
Fans who register with us will be the first to read our news and the progress of this exciting Tricorder development and, later, where and when to purchase it. You can catch up with the story so far here on this blog, but if you haven’t already done so, why not register your interest in the Tricorder – you’ll then receive a personalised registration certificate and early access to these updates (before we publish them on our website).
I am an electrical engineer and I honestly can’t wait to see one of these. Star Trek was one of the catalysts of me entering into a technology field.
I was brought up on the Star Trek franchise and just like the other super passionate fans, I always wanted working models of the tools from the series. I have the communicator and the phaser. This will make the perfect trifecta of Star Trek props. One more addition to the man cave.
Based on other items I have purchased, this will be well worth the wait.
Another great set of reveals. Love it! Can’t wait to see more details!
A question: I’ve noticed in a few of the updates now that there is a ‘honeycomb’ design built into parts of the Tricorder. Is this a tie-in with WandaVision? Are you making the Star Trek/X-Men crossover CANON?!?
😉
Seriously, though, what is the purpose of the honeycombs? Strengthening the cover? If so, why not just thicken that entire section instead of creating a hitherto non-existent latticework? Or is that the plan – to cover the honeycombs with another piece? In other words, will they be visible on the finished product?
Thanks!
Thanks for the enthusiasm! The honeycomb was indeed added to strengthen the cover – for injection-moulded parts, increasing the thickness is generally not a good idea, as it tends to cause warpage and sink marks. We chose the honeycomb pattern after seeing it in a number of places in the Star Trek Original Series set tour, for example in engineering and in the corridors.
“increasing the thickness is generally not a good idea, as it tends to cause warpage and sink marks.”
I suspected *something* along those lines. Thanks for enlightening me about the process that goes into your wonderful recreations! 🙂
“We chose the honeycomb pattern after seeing it in a number of places in the Star Trek Original Series set tour”
Ah, that makes PERFECT canon sense! Bravo on integrating those TOS details into the production where you needed to enhance the original. Can’t wait to learn more! Monday’s email can’t come soon enough. 😀
Actually, Monday is a public holiday here in the UK so the next newsletter is scheduled to go out on Tuesday 4th May.
A public holiday on the 3rd? Wow. I didn’t know the UK took “Garden Meditation Day” so seriously!
https://ngs.org.uk/garden-meditation-day/
Have a perfectly Zen day, man. 😀
This is just a fantastic replica, I’m just gonna say that. Like many people here, I have long-awaited a real function tricorder. I like others have said, Star Trek has been a huge influence in my life. It influenced me to be an electronics engineer and an IT professional. At 52, I still get excited for the tech I grew up with on the small and big screen coming to life. The Wand Company is making that happen for all of us. I proudly display my phaser, communicator and phaser rock in my den. People ask where they came from and I tell them. I’ve built realistic props for decades out of metal and any other materials I could find, but Wand does an outstanding job!
To me, the KEY to making this the most ACCURATE and functionally authentic , is to have VIDEO / AUDIO record and playback. my TINY digital camera has those features, so with ALL the room in this replica, that should be NO issue…this is the ONLY time any company will the opportunity to GET THIS RIGHT.If this is not included, then in my view, the BOAT WAS MISSED..
I am sorry, I think you’ll have to plan for a missed boat then as we have not designed a camera into our tricorder. However, the tricorder will be able to record and playback audio… so maybe not a completely missed boat. The issue was that the screen-used prop had no obvious camera. That said, there are of course very small cameras that could fit and possibly almost invisibly (although not completely invisibly). The thing is that a camera brings with it some other overheads in terms of cost and a significant increase in the development effort required to enable capturing, compressing, recording, storing, and then playing the video back. In any case, we have other plans for creating a rich and immersive experience for owners of our tricorder, some of which will be unexpected, but that we believe the vast majority of fans will fully appreciate and enjoy. We will be describing those functions in detail in future newsletters, but the next newsletter that will be emailed out on Tuesday, May 4th will describe the functional blocks that make up the tricorder, and will start to give some ideas into the scope of the functional and mechanical features that we have developed for it and thus what it will and will not obviously be able to do.
May the Fourth? Taking over Star Wars day, eh? Good marketing! 🙂
Don’t worry about not having video recording capacity. Given the design and the price point, I knew you weren’t going that route. Most people don’t realize how truly complicated and costly it can be to provide *good* recording capabilities. Moreover, the Tricorder is not the best platform for taking images or videos in the first place. Essentially, one would be shooting blind and hoping for the best. To me, it would be like trying to take good pictures with your smart watch. The results would not be very good.
May the 4th… haha yes a happy coincidence, if you believe that! But it is a cool SciFi crossover. Re the video, yes, that was our thinking entirely. There is so much more to the tricorder that would be out of place anywhere else.
I’m not really concerned about video, for reasons you’ve already covered above. I’m actually nerdgasming over the ejectable discs. That’s a truly unique and unexpected feature. I’ve got the phaser and communicator, so I can’t wait to complete my set. Any vague idea when you’re releasing the product yet?
Chris, thank you so much for your thorough responses to these posts. I’m loving the email updates as well. Can’t wait for the next one this Tuesday!
Thanks, we’re really enjoying putting these posts together, so it is great to hear that you are enjoying them.
Hi Chris,
I’ve registered my interest in the tricorder a couple of times now but am still not receiving your updates In my email. I happened upon them while surfing the net. Is there something else I need to do to receive your updates? Thanks… I can’t wait for the tricorder to be released, it looks and sounds amazing.
I’m curious, will there be any ability to add or modify what sensors are included? I’m guessing probably not, but I figured that would be pretty cool.
Well, that is not currently on the cards, because that level of modularity (which we did discuss early one and would no doubt be really cool from a functional and completest world view), results in an enormous amount of additional development effort that is hard to justify and actually accommodate within a realistic project timeline… for our team anyway. But I guess with some exotic skills anything can be hacked…
Chris and Richard
Thanks so much for these interactions with your fans/customers. I don’t know of any other company that has done that during the development of a new product. You did the same with the Phaser and Communicator and please know that it’s really appreciated.
Great Work!
Chris and Richard
There are already people on the prop forums saying they’re going to buy as many Tricorders as possible. I really hope you limit these to one per customer (at least in the initial run) to give as many people as possible a chance to own this awesome replica.
Please don’t worry, there will be a pre-order window that will tell us how many to make to meet genuine demand. As you might have gathered, the tricorder is a very important product for us. As fans ourselves, the whole user experience is something we will do our very best to get right all along the line, as you can see, starting with how it looks, then how it works and feels all the way through to the purchase experience and beyond. If everyone that wants one is able to get one, then some people buying more than one for their needs is great because it means we can make more products and the tricorder will be more successful.
Thanks Chris! My concern was them selling out immediately to hoarders that only intend to sell them on eBay layer for 10 times the price.
Happy Star Wars Day! Got the greatly anticipated Update #5 in the mail. Thank you! 🙂
One thing jumped out at me. Is it true that the Hood will rotate a full 180 degrees, as stated? Or was that a typo and the hood will just open to its normal 90ish+ degrees? In other words, is the hood ‘fully open’ when the faceplate essentially faces forward? Or is the hood capable of ‘fully opening’ to a point where the faceplate is essentially facing straight up?
When will it be ready..?
We are not 100% sure yet, but we are aiming for some time this year. The pandemic has played havoc with component supply and we are currently trying to get some of the major long lead time components on backorder so they don’t become the rate-limiting factor.
As you are registered, you will be one of the first to know when we are opening for pre-orders. We won’t do that however until engineering production has been completed and we are fully happy with the tricorder and it is functioning how we expect, so we can go into full production with confidence.
This is truly amazing! I can’t wait to see it coming off the production line. Any thoughts on making the software open-source or at least so that enthusiasts can contribute features?
THIS^^^^^ x100!
I hate the long wait time, but I’m grateful for the transparency on your part, Chris. I know the quality will be worth the wait (I have a communicator and phaser). You guys are really outdoing yourselves on this one.
Hi Chris,
I am back again may still have some interest for your Star Trek Tricorder & how soon it will be ready.
Would you have a pre- idea of what cost it will have when finished with price tag. Star Trek has just
Celebrate 55 years ago started September 8, 1966 – 2021. Have a good weekend coming up.
Donald S.